摘要:利用数值计算的方法对涡轮流量计内的三维湍流流动进行建模和基于N-S方程的仿真分析。数值计算采用k-ε模型来模拟湍流流动,得到涡轮流量计的内部流场三维流动形态,并分析其内部的流动规律、流速和压力分布;以三维湍流仿真的仿真结果为依据,对前导流器进行了优化。结果表明:流线型前导流器能降低整个流量计的压损。
电池供电涡轮流量计是速度式流量计的一种,其测量准确度高,复现性和稳定性均好,量程范围宽,量程比可达(10~20):1,线性好,耐高压,压力高,压力损失小,对流量变化反应迅速,因此它被广泛应用于石油、化工、电力、工业锅炉、燃气调压站、输配线管网天然气、城市天然气管网等领域,并已被广泛应用于贸易计算。气体涡轮流量计的气体流动是*其复杂且非稳态的,若通过单纯的经验公式理论分析与流量计性能试验研究的常规方法确定其设计参数,难以得到理想的效果。流量计内部流场的流动状况直接决定流量计的性能,因此了解涡轮流量计内部流场可以改良和研制高性能涡轮流量计产品。国外很早就进行了仿真研究,国内专家也进行了理论和实验研究。通过CFD仿真研究了切线型涡轮流量计;利用数值模拟研究液体粘度对涡轮流量计的影响,利用Fluent对涡轮流量计的流场进行模拟,分析获得压力场和速度场,全面了解流量计的流场情况,得出指导性和方向性的结果,可以帮助选择性能*佳的方案。本文通过Fluent模拟气体涡轮流量计的内部流动,分析其内部的流动现象,获得流量计内部的速度场和压力场,并对前导向器进行优化。
1、涡轮流量计的原理
涡轮流量计主要由壳体、前后导流器、叶轮组件、磁电感应转换器等组成,其原理如图1所示。当被测流体通过流量计时,流体通过导流器冲击涡轮叶片,由于涡轮叶片与流体流向间有一倾角θ,流体冲击力对涡轮产生转动力矩,使涡轮克服机械摩擦阻力矩和流动阻力矩而转动;在力矩平衡后转速稳定,涡轮的旋转角转速与通过涡轮的流量成正比;涡轮转动时,使通过线圈的磁通量发生周期性的变化而产生与流量成正比的脉冲信号。
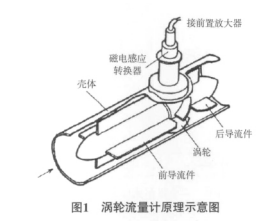
2、计算方法与模型选择简化
2.1仿真模型建立与网格划分
根据实际情况,本文选择普通的DN150气体涡轮流量计为研究对象。为了消除涡轮流量计入口的脉动流,在流量计的入口加了0.5倍长度的直管段,出口也加了1倍长度的直管段。按照仿真模型的结构特点,采用分块建模的方法,将模型域分为前导流件、叶轮、支架、后导流件及前后直管段等6部分。流量计参数如表1所示。

根据计算域的复杂程度,前、后导流件及叶轮旋转区域采用四面体非结构化网格,网格数为370 000。支架及前后直管段采用结构化的六面体网格,以节约计算资源,网格数为350 000。网格划分如图2所示。
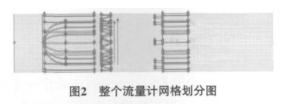
2.2湍流模型的选择与简化
本研究基于的控制方程为粘性、不可压缩的N-S方程。
连续性方程为:
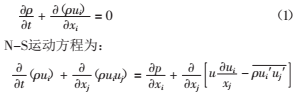

湍流模型采用Reynolds Stress模型不收敛,采用Spalart-Allmaras精度不够,故湍流模型采用标准的k-ε
模型进行仿真。连续性条件通过压力修正得到满足。方程的求解方法采用SIMPLE算法,方程离散过程中采用二阶迎风格式离散。
针对气体涡轮流量计的流动特点,对模型做如下简化:由于本文入口边界为速度入口且入口速度都小于50m/s,速度的变化对气体的密度影响很小,因此假定为不可压缩流动;将叶轮旋转部分设定为相对旋转坐标系后,流动为定常。仿真过程边界条件选择如下。
入口边界条件:虽不知道压力条件但能容易得到入口速度,故选择速度入口为:
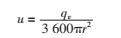
式中:r为管道半径;qv为不同流量点的流量;u为对应流量点的管道平均流量。给定流量点500m3/h,入口速度为7.86m/s。
出口边界条件:自由出流,其他边界均为壁面。采用Fluent中的MRF(多参考系)模型,给定叶轮的旋转角速度进行计算。数值仿真的介质为室温下的空气。
3、仿真结果及分析
3.1速度场分析
(1)速度场沿轴线的分布中心线剖面速度分布如图3所示。
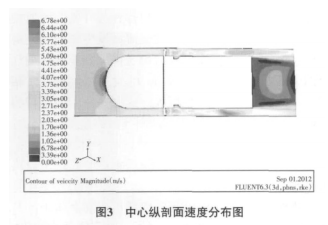
由图3可以看到,涡轮流量计内部的速度场近似于中心轴线上下对称,前导流器圆弧型端部中间部分速度明显减小,靠近管壁速度增大。气体进入前导流器后,由于球面中间部分的阻挡,导致靠近圆弧面速度减小,且圆弧面的存在使流动的横截面积减小,环形通道的流速加快。
(2)叶轮进出口截面上的速度分布叶轮进出口截面上的速度分布分别如图4和图5所示。
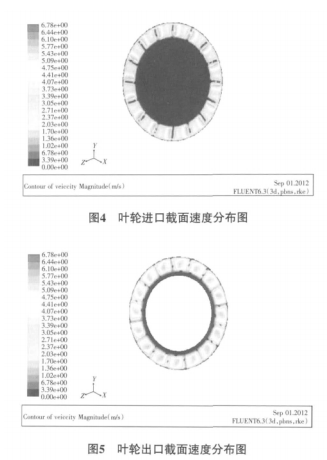
从图4可以看出,在叶轮的入口截面上,速度轴对称分布,这是由于所有叶片形状完全相同且成中心对称分布,以及前导流器成中心对称并与叶轮叶片数相同,气流流经叶片时会与叶片迎流面发生碰撞而使得气流速度减小,而背流面气流由于截面减小从而使气流加速。对比图4和图5可以看出,速度场结构非常相似,后者的速度大小明显增大。这主要是因为旋转的叶轮对气流的牵连作用使得圆周方向的速度加大。
3.2压力场分布
中心纵剖面压力分布如图6所示。叶轮进出口压力分布如图7、图8所示。
从图6可以看出,流道的内部压力逐渐减小。其中,前导流器球面压损大,环形通道几乎无压力损失。其余部分压力分布比较均匀。
由图7、图8可知,叶片迎流面上为高压区域;沿着流动方向压力逐渐降低;叶片压力面上为低压区域,沿着流动方向压力逐渐增加。在叶片的入口截面上叶片前缘有明显的压力过渡,这些均说明叶片迎流面形状对叶轮旋转特性有影响。叶片前缘压力较高,这是因为气流在流动时,*先与叶片迎流面的前缘发生碰撞,做功较大的缘故。叶片后缘压力也较高,是因为受边界层的影响。
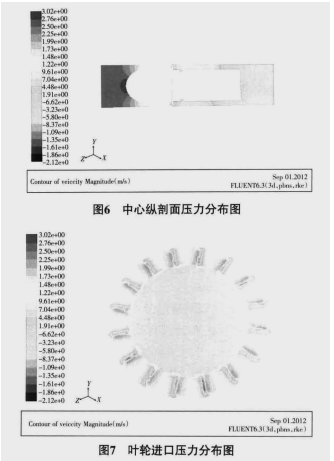

4、优化后的流场
分析气体涡轮流量计的内流场后,发现前导流器的结构对流量计的压损影响*大,为减小入口气流对前导向器中心体的碰撞影响,降低进口的压力损失,对前导向器做如下改进:将圆弧型前导流器改为流线型。通过对图中的模型重新进行流态仿真,优化后涡轮流量计内部流场较优化前更加均匀稳定。改进前后中心剖面压力等值线分布如图9、图10所示。
http://www.jskmyb.com/uploads/20170923/9.png
从图9、图10中可以看出,改进后前导向器的压力损失更均匀(梯度较小),并使其后各部分的压损减小,从而降低了涡轮流量计整体的压损。
5、结束语
为研究涡轮流量计测量过程的流态分布,本文优化了内部流道,得到压力损失小的涡轮流量计。通过对原型涡轮流量计内部气体流动规律的分析,得知前导向器的压力损失不均匀(压力梯度很大),可以将圆弧型前导向器改为流线形前导向器,降低涡轮流量计的总压损,从而实现了涡轮流量计的气流通道的优化设计。